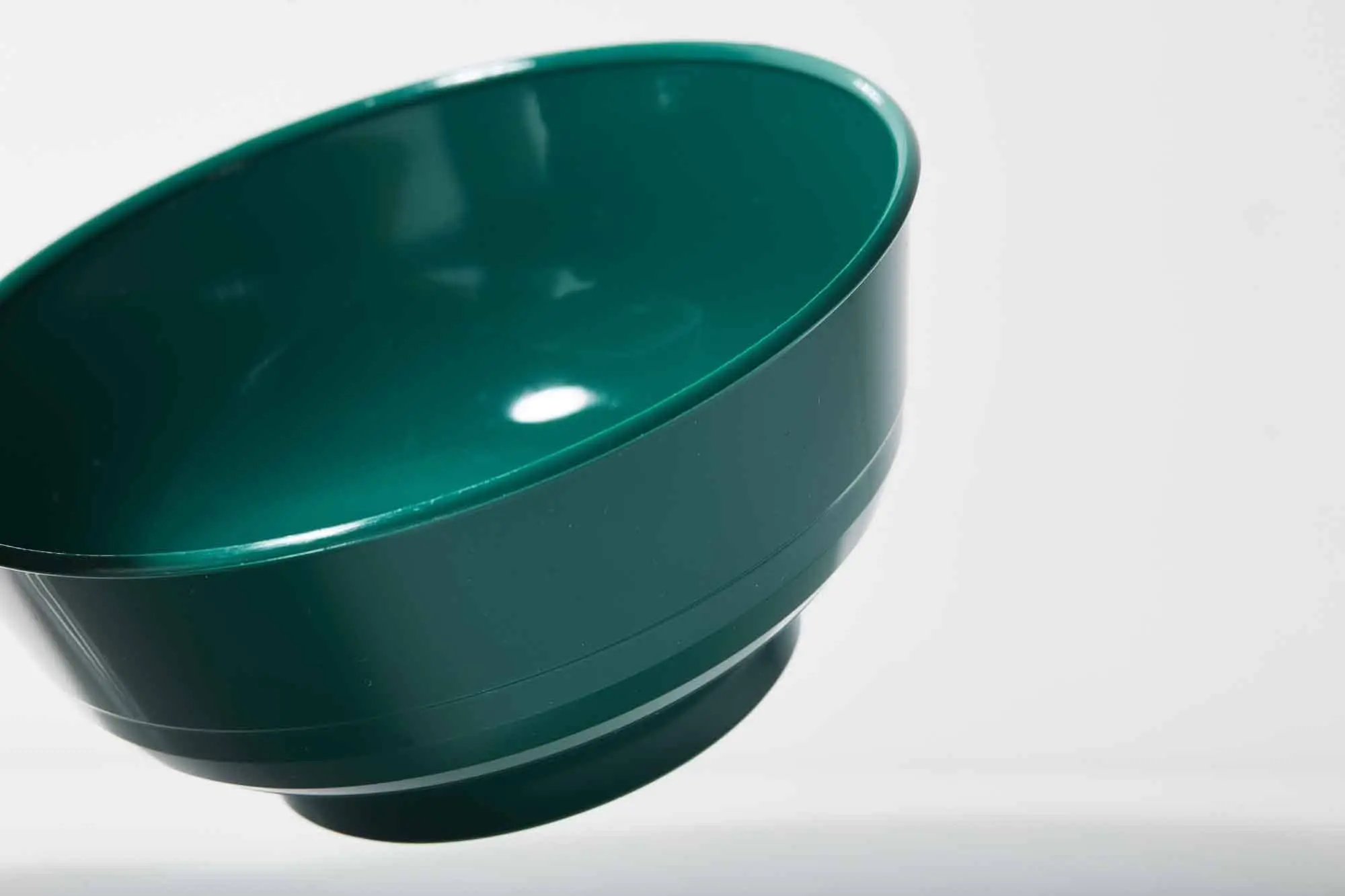
Alternative Plastics: Is It Possible to Reduce Dependence on Fossil Fuels?
Plastics have transformed our daily lives, providing versatile and convenient solutions for a wide range of applications. However, the excessive use of traditional plastics, derived from fossil fuels, has a negative impact both in terms of CO2 emissions and in terms of pollution at a local level. To address these challenges, the industry is gearing up to propose alternative plastics with reduced environmental impact thanks to the use of more sustainable raw materials and processes.
What are the main directions of development for these alternative plastics?
Materials can be designed to have a reduced environmental impact compared to conventional plastics. This can be achieved in different ways, depending on the application area. If in disposables the direction is the elimination of plastics tout court, in other areas, where plastic has undoubted environmental advantages, such as durability, impact resistance and above all lightness, the aim is to develop alternative plastics to traditional ones through the use of raw materials from renewable sources (bio-based) or recycled.
Bioplastics can be biodegradable or non-biodegradable; they help reduce dependence on fossil fuels and generally have a lower carbon footprint than their petrochemical counterparts.
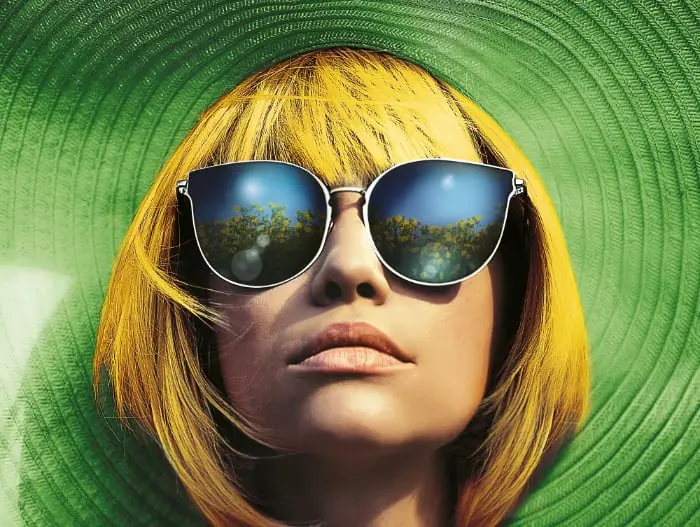
An interesting case study is the development of optical lenses with bio-based, bio-attributed content. Evonik has engineered a transparent polyamide, specifically optimized for the optical industry and based on the mass balance approach, that results in a 40% share of bio-based raw material in the polymer. In combination with a manufacturing process that uses entirely renewable energy sources, a 50% reduction in the carbon footprint is achieved. The halving of the carbon balance is confirmed by a certification from TÜV Rheinland.
Alternative plastics with bioattributed content have completely identical performance to their fossil-based counterparts and can therefore also be used in applications that require specific performance, such as in the eyewear sector.
Recycled plastics, on the other hand, derive from the recycling of existing plastic materials, which not only reduces the amount of plastic waste, but also the need to produce new plastic, saving resources and energy. The carbon footprint of recycled plastics is lower precisely because the entire phase from extraction to production of the granule is cut off the impact calculation.
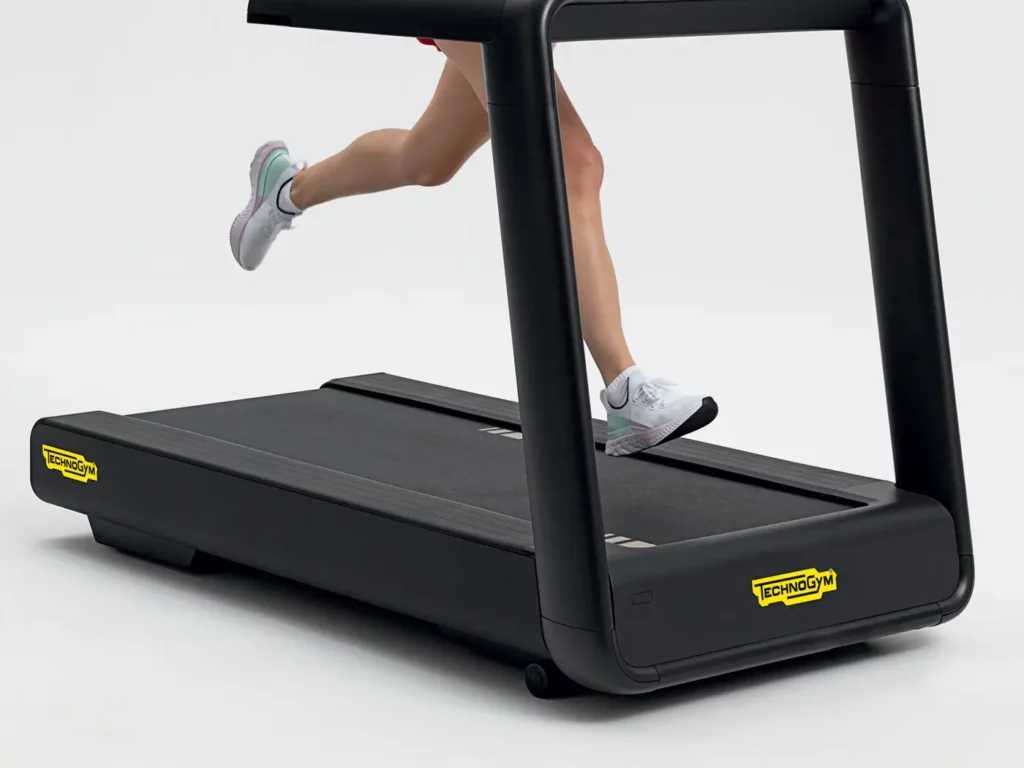
More and more companies are offering products with recycled content, even in technical sectors with high performance requirements. This is the case of Technogym, which presented a series of fitness equipment to minimize environmental impact right from the production stage. The plastic components are made of ABS-based thermoplastic resin with a 60% circularity rate, resulting from the mechanical recycling of household, electrical and electronic waste. The use of recycled materials allows the recovery of approximately 7 kg of plastic per piece and translates into a 50% reduction in CO2 emissions compared to the use of completely virgin materials.
Opening image: Cellulose-based bioplastic with 45% renewable carbon that offers high performance and low environmental impact for demanding applications. From Material ConneXion library