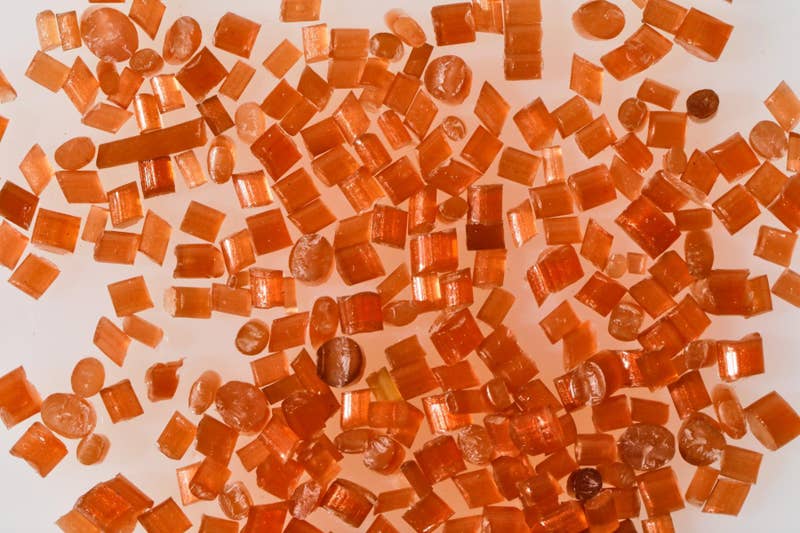
The three materials of the month: alternative plastics
Plastics are a very broad family of materials that have replaced most other materials in the last century. Being virtually eternal materials, plastics have soon proved to be extremely polluting if mismanaged, triggering a demonization process.
While the direction is to ban them for applications in disposable goods, recycling is promoted and seen as the most viable option for durable goods.
Growing attention to the environmental issues generated by the over-consumption of plastics is also spurring manufacturing companies to come up with more sustainable alternatives plastics. More and more, for example, are bio-based versions of common plastics such as PE, PET and ABS; there are also numerous polymeric materials with pre- or post-consumer recycled content, and those made from the recovery of agricultural waste.
Material ConneXion’s database is constantly being updated on these topics. Here are three materials recently added to the library that represent some of the most significant directions of innovation in the area of alternatives plastics.
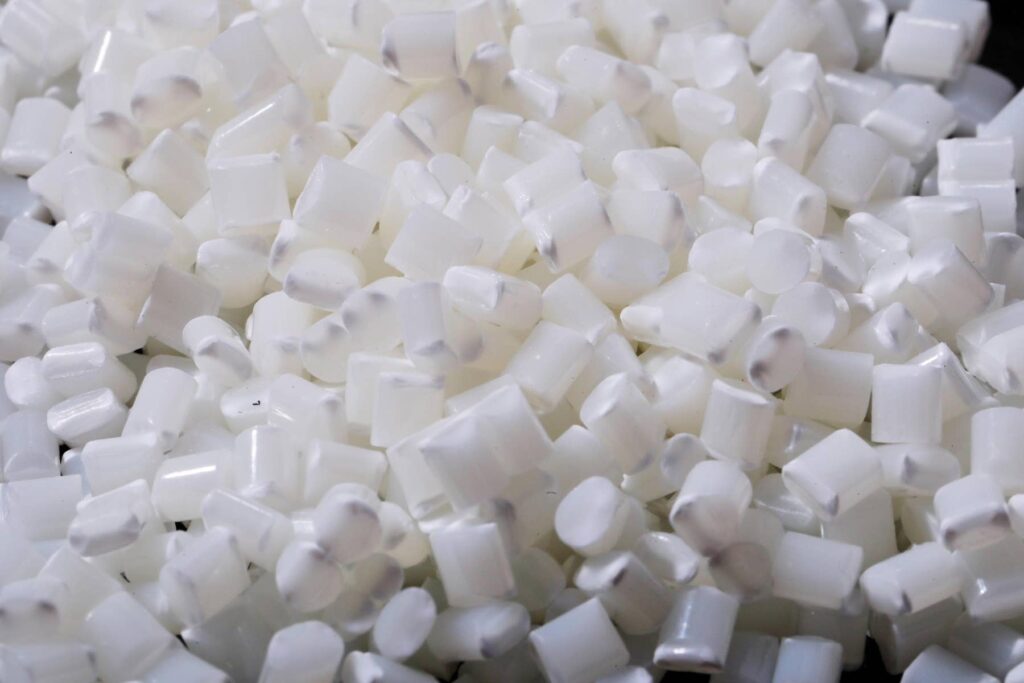
Image courtesy Material ConneXion LLC
The first is a 100% bio-based thermoplastic material that can replace virgin ABS without the need to modify molding processes or parameters. Produced by replacing petrochemical-derived raw materials with bio-based materials from non-food sources, this bio ABS offers performance equivalent to virgin ABS regardless of the percentage of biological content. It lends itself to a wide range of applications, including accessories, consumer electronics, cosmetics, home appliances, medical devices, packaging, safety equipment, tableware and toys. The material can be processed by various methods such as additive manufacturing, blow molding, extrusion, injection molding, and rotational molding.
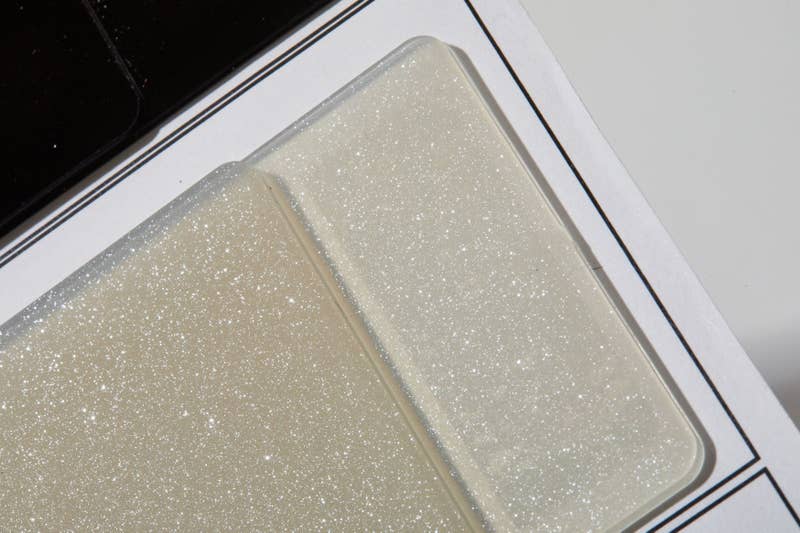
Image courtesy Material ConneXion LLC
Based on the same principle, the next material is a polycarbonate resin composed mainly of plant-derived isosorbide. As an engineering plastic, it has the advantages of both conventional polycarbonate resin containing bisphenol A and acrylic resin. Specifically, it exhibits the same transparency, low birefringence, and scratch resistance as acrylic resin, with improved resistance against weathering/ yellowing typically seen in polycarbonate resins. The material is available in pellet form suitable for injection molding, extrusion, and film production. It can be produced in metallic colors, and it is possible to customize its mechanical properties and color. In addition, the material can be used in various situations, both indoors and outdoors, without the need for painting due to its excellent colorability and UV resistance, thereby reducing CO2 and VOC emissions.
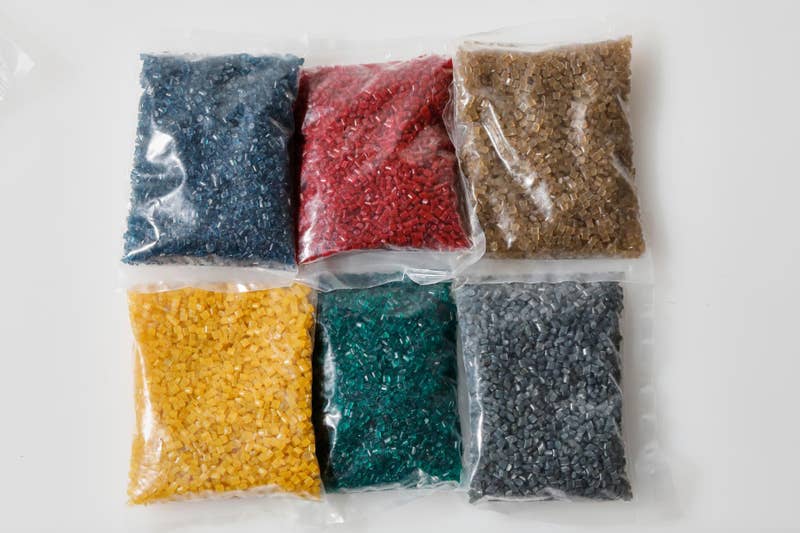
Image courtesy Material ConneXion LLC
Pictured above is an alternative plastic represented by pellets made with 70-80% recovered cellulose acetate from cigarette filters and 20-30% plant-based additives. To produce the resin a proprietary mechanical-chemical process removes all solid waste from cigarette butts, efficiently eliminating all toxic substances. The recovered fibers get compounded with plant-based, biodegradable plasticizers and then pelletized using conventional plastic industry techniques. The pellets have diameters between 3-5 mm and meet the conventional physical, mechanical and aesthetic properties of other acetates on the market. They can be easily pigmented with various intensities and levels of transparency, and processed by injection, extrusion, and compression. For every kilogram of cellulose acetate recovered and transformed into the product, up to 5,600 cigarette butts can be removed from the environment. Additionally, the material’s LCA demonstrates a carbon footprint 36% lower than virgin cellulose acetate. Applications include eyeglass frames, tool or instrument handles, buttons and other accessories.