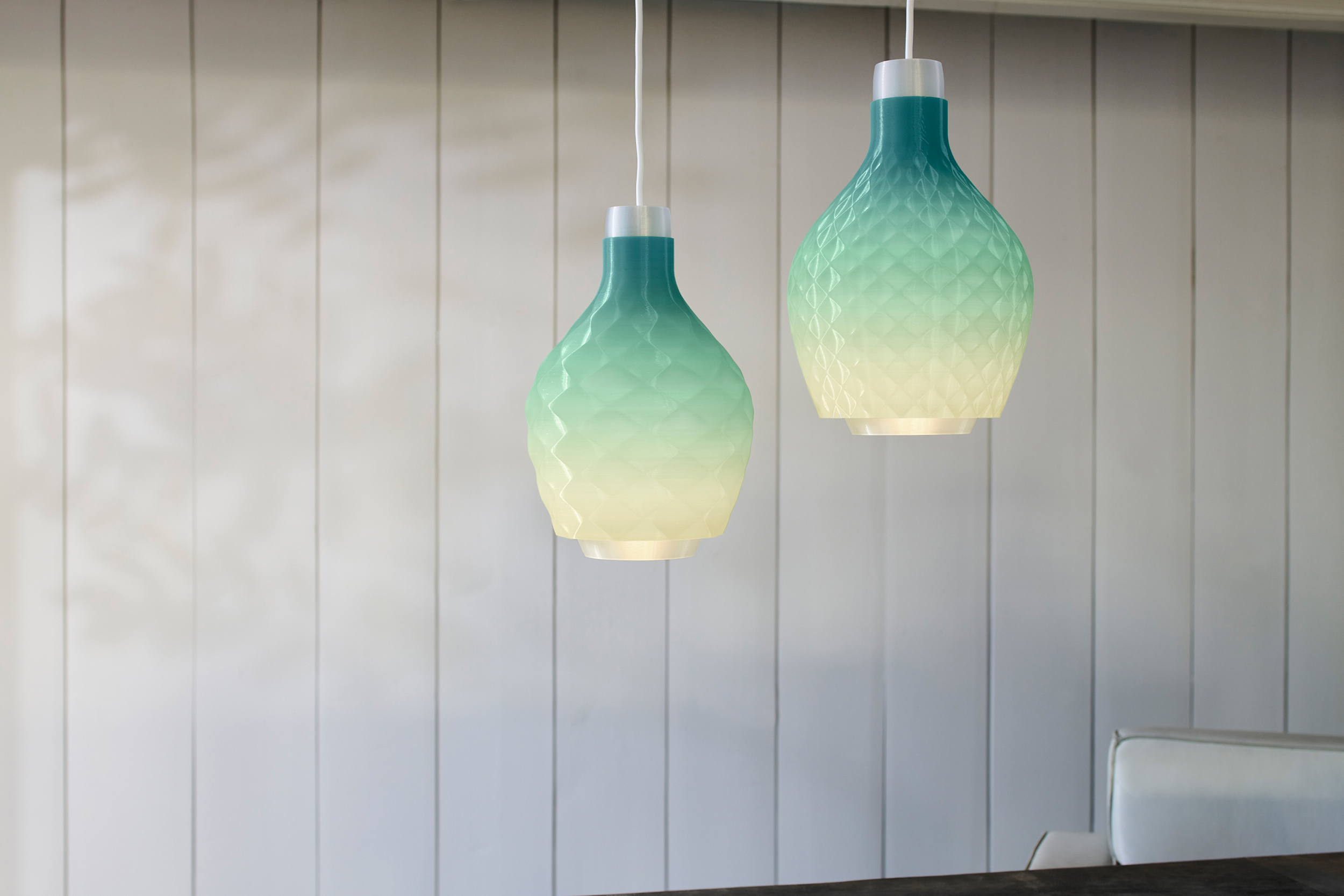
The three materials of the month: 3D printing
With the latest developments and fine tuning of 3D printing technology and machineries, new scenarios for product development and design are spreading across industries: From domestic consumer goods to fashion design, from high-end mechanical applications to furniture and light design, new solutions emerge to support designers’ creativity in the perspective of improved performance and eco-conscious design.
Material ConneXion, constantly explores the world of innovative materials, grouping them within a single, easy-to-consult directory, capable of providing information to make aware choices. Here are some of the latest materials recently entered into the library and which represent three of the most significant directions of innovation in the sector.
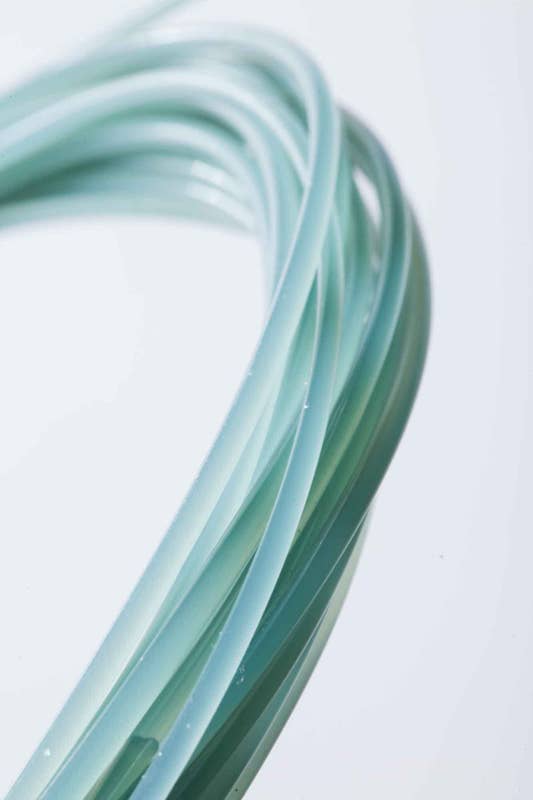
This 3D printing filament is made from discarded polymer fishing nets to reduce the amount of ocean plastic pollution produced. Fishing nets tend to be set aside as waste when they have been physically damaged during fishing, or because they have been coated with an algal biofilm. This fishing net waste, typically made from nylon 6 (PA6) monofilament, is collected and then processed using a proprietary washing and shredding process to thermo-mechanically recycle it into clean and dimensionally stable filaments. The process of producing the renewed filament is designed for minimal chemical and energy use, with both water and gaseous emissions considered throughout the entire process. Interestingly, the filaments can only be supplied in the colors of the original fishing nets, offering a fascinating palette in the blue-green.
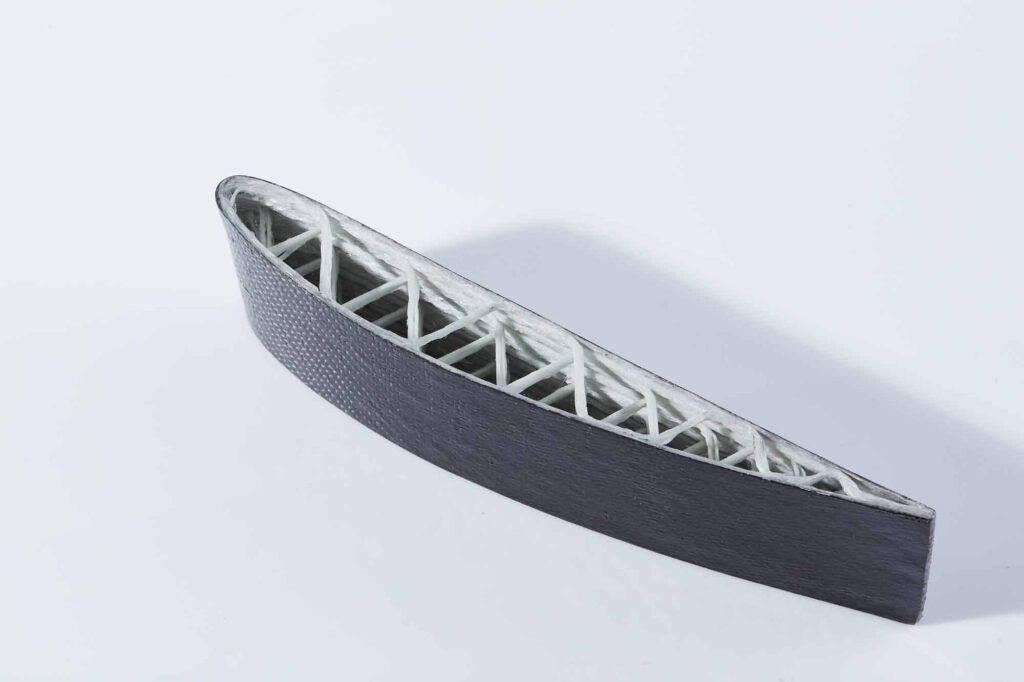
This proprietary 3D printing technology leverages rapid curing resins paired with continuous fibers, creating a moldless, ‘Out of Autoclave’ (OOA) composite manufacturing process. This unique combination of composite materials with the latest technology in 3D printing and robotics offers new design possibilities for manufacturers and consumers to create complex composite structures, without other support materials. While traditional 3D printing and the composites manufacturing industry are plagued with the limitation of only being able to stack 2D slices; this technology can discretely print fibers to accommodate loads in all three dimensions.
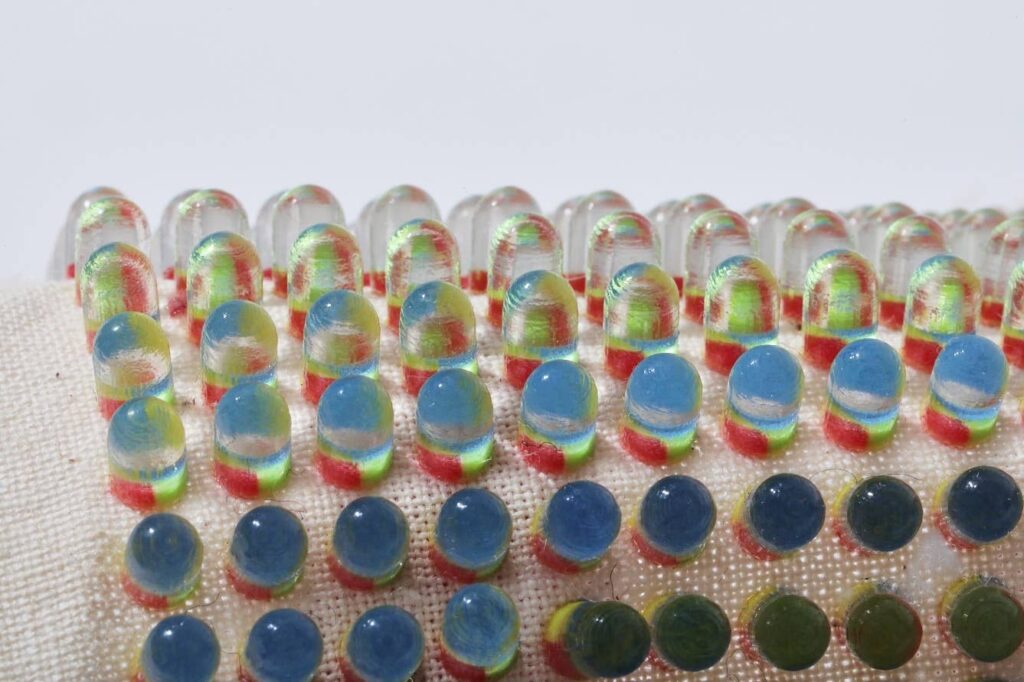
Here you see a novel 3D lenticular printing process for flexible and rigid substrates. Lenticular printing has existed in the design world for years; however, it has always been restricted to two dimensional designs. Designers, with the help of advisors, wanted to take advantage of the multi-material capabilities of the latest 3D printers available to create something unique. Utilizing different materials, they discovered how to merge physical and digital fabrication to create entirely new optical properties and user experiences. The technique to achieve the lenticular printing relies on several different functioning layers, instead of just an outer surface texture, and requires information to be embedded into each three-dimensional pixel. This technique can be used to create a variety of 3D lenticular designs, such as shifting patterns, interactive written content, and even touch-sensitive visual effects using flexible materials.
Cover image Image Lamp design by Philips My Creations