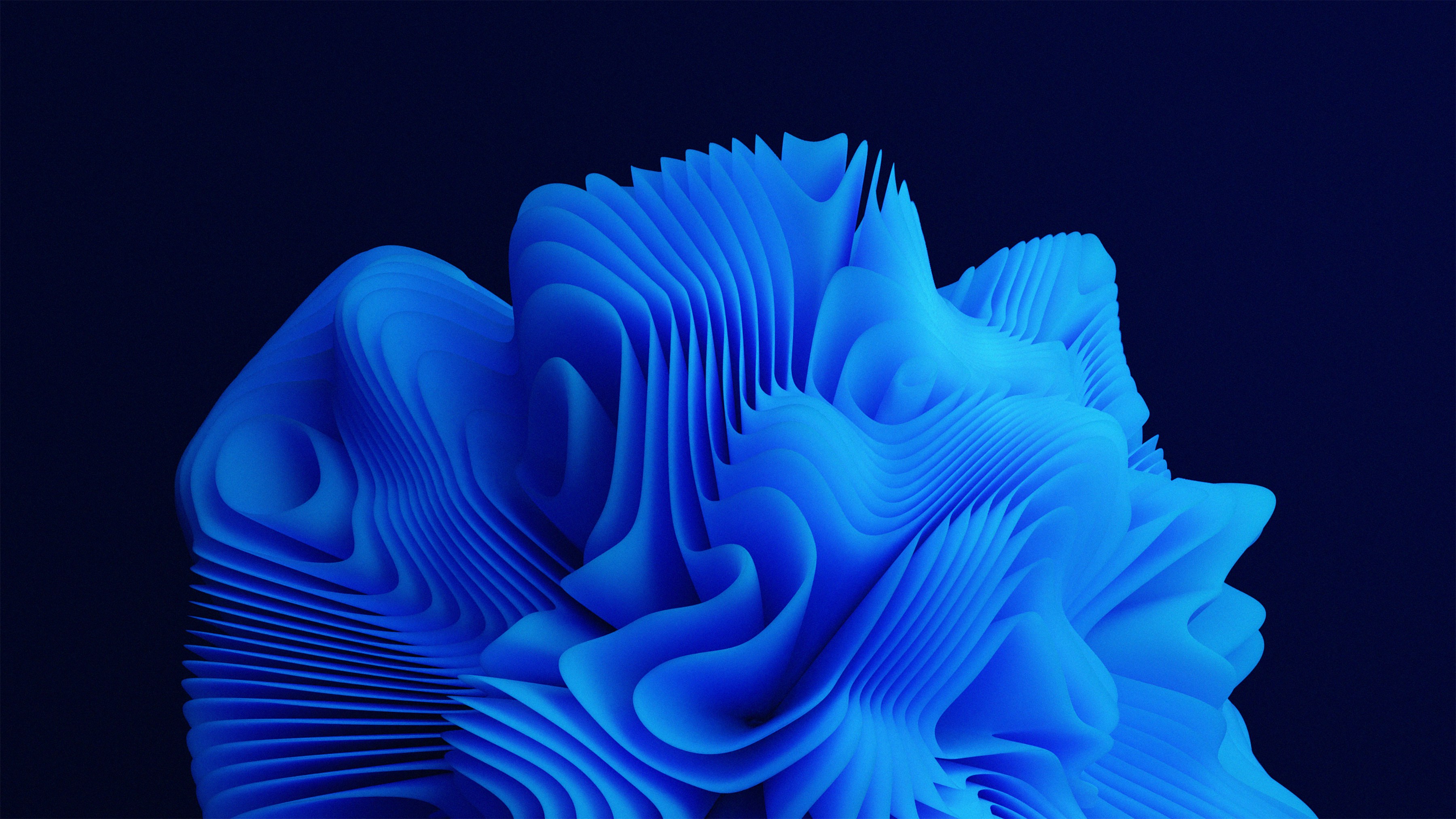
Optimizing the use of 3D printing materials through artificial intelligence
Data has long been used in engineering design to determine the shape of a product so that it can meet specific performance requirements. In essence, a virtual alias is created that is used as a predictive tool to evaluate the behavior of certain structures. 3D printing then intervenes to physically create these structures, as prototypes but also with actual production.
Some examples
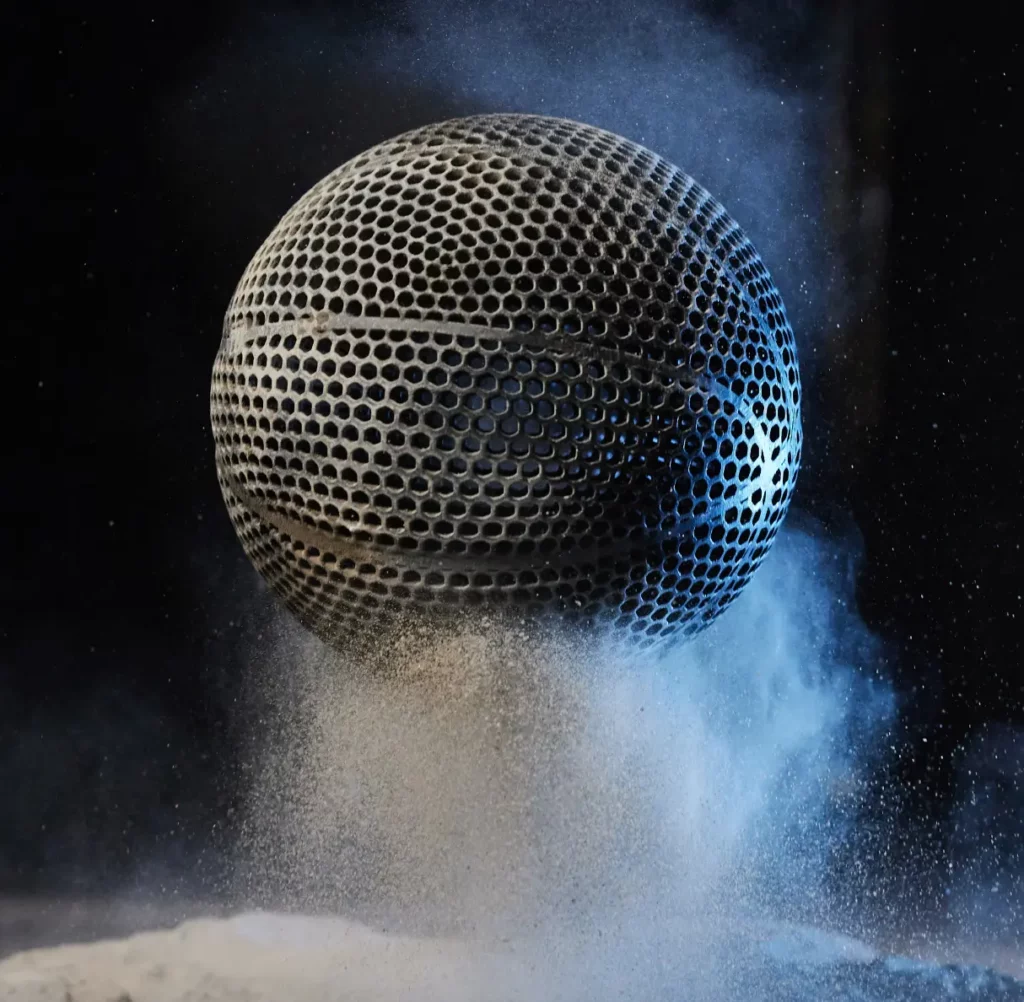
Starting from this principle, and with an approach similar to the one already used for the creation of “airless” tire concepts, Wilson has developed a basketball that uses a hexagonal mesh structure 3D printed using SLS – Selective Laser Sintering. The structure, first developed and tested digitally, behaves like a metamaterial and allows the ball to bounce just like a standard pressurized ball. The absence of pressurized air means less or no maintenance: the ball constructed in this way does not lose its bounce because it does not deflate. The prototype was created in collaboration with EOS, a historic company in the development of 3D printing machines and materials, which created the functional prototype.
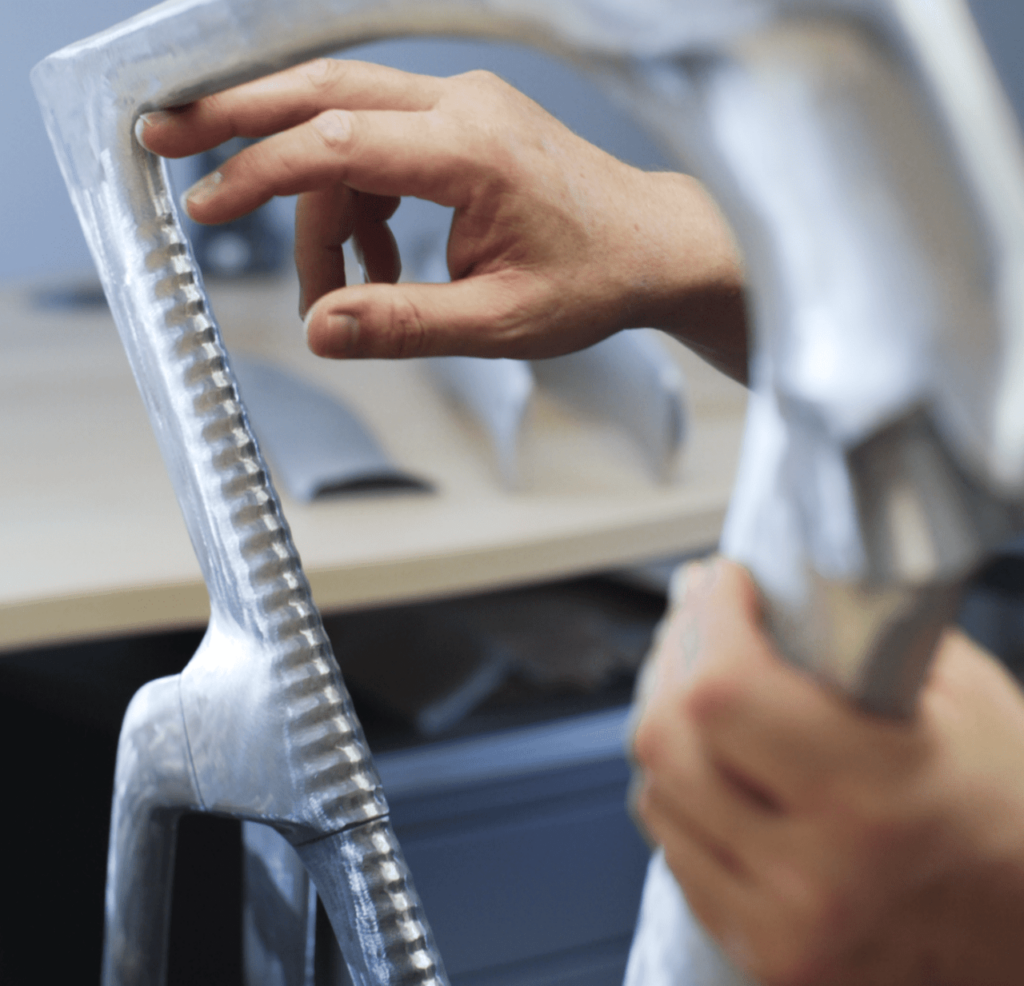
Also in the sports field, Pinarello recently presented Bolide F HR 3D, a 3D printed bicycle that will be used by the Italian team at the Paris Olympics. The Bolide F HR 3D frame and fork were made of Scalmalloy, a high-strength alloy of scandium, aluminum and magnesium. Also in this case, the collection of data regarding the stresses that are applied to the frame during the race and optimal aerodynamics allowed us to design a shape that can respond very precisely to the specific needs of this product. For example, the Scalmalloy frame is slightly heavier than traditional carbon fiber ones; but also more resistant and stable, characteristics that are particularly useful for male athletes, who exert greater forces on the frame. The horizontal grooves on the seat tube, inspired by humpback whale fins, help reduce aerodynamic drag, but they can only be achieved through 3D printing, which is a perfect tool for making complex structures tangible.
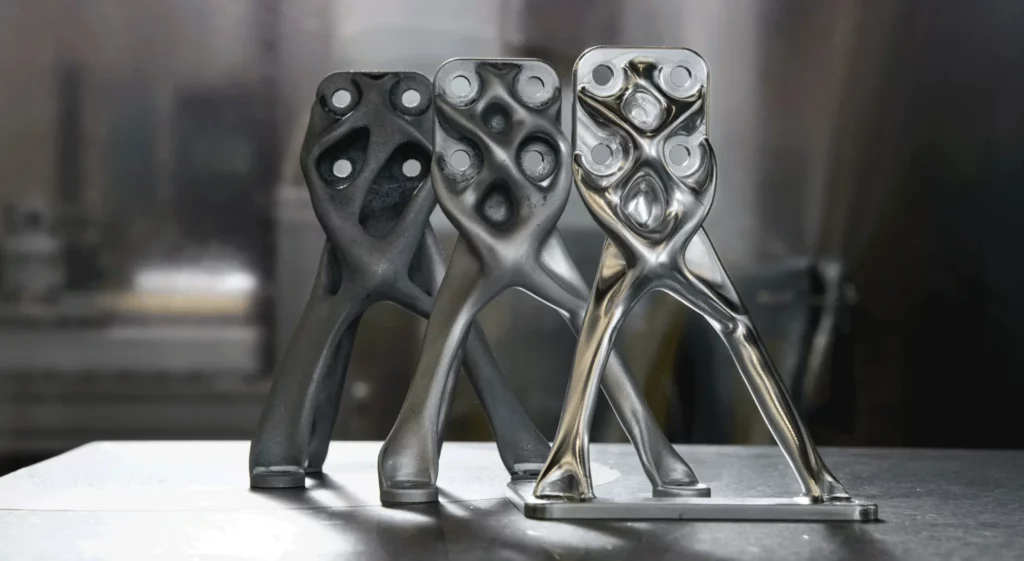
Within this approach, new tools such as AI-based software can be of great help in processing countless iterations in a short time to optimize the characteristics of a structure and even a material.
NASA, for example, has started using AI to develop some components that are significantly stronger and lightweight. The process, called “Evolved Structures,” takes a fraction of the time it takes NASA’s “human” engineers and is based on a generative algorithm designed specifically to create metal brackets and supports. The AI-based software allows for a huge amount of possible variations to be virtually tested, ultimately selecting the most efficient one in terms of mechanical resistance to weight ratio.
Cover photo: SIMON LEE by Unsplash