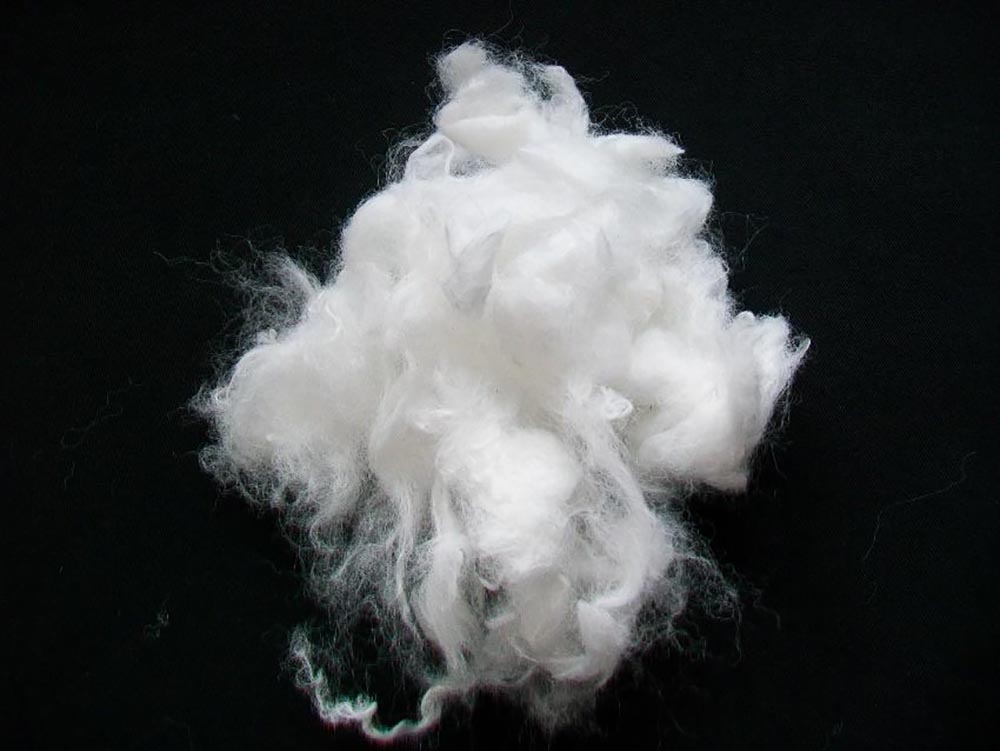
Cellulose: an extraordinary material for the future of textiles
We’ve been talking about cellulosic fibers for a long time, writing about the latest developments and challenges that the textile industry is going through within its recent commitment towards more sustainable processes and solutions for a fast, high-demanding market.
We discuss here some of the most common cellulose-based fibers and present the most recent achievements in this field. Many of these fibers are already well-known, the difference lies in the sourcing of the raw materials and the processing techniques.
Why such an interest on cellulose? Well, cellulose is an organic polymer that presents unique physical properties, such as great tensile strength, water and solvent resistance, lack of odor and biodegradability that make it the most abundant, reliable and renewable resource for the textile industry.
It is found both in vegetal fibers such as cotton, hemp, jute, kenaf and similar that get usually and traditionally worked mechanically to produce yarns and thus fabrics, but it is also the main component in man-made fibers that started developing in the last two centuries.
The first successful process for industrial scale application of man-regenerated cellulosic fibers was that of the Viscose method, that became dominant around the 1940s. Despite starting directly from wood pulp, this process is known to be significantly pollutant due to the intensive use of chemicals and solvents such as sodium hydroxide.
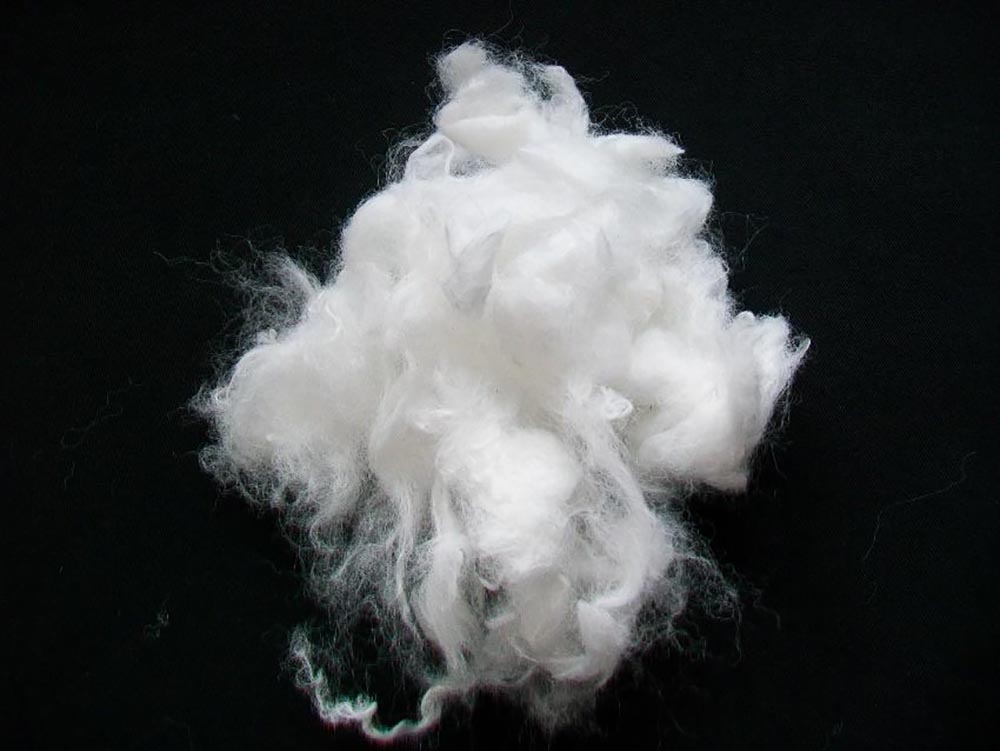
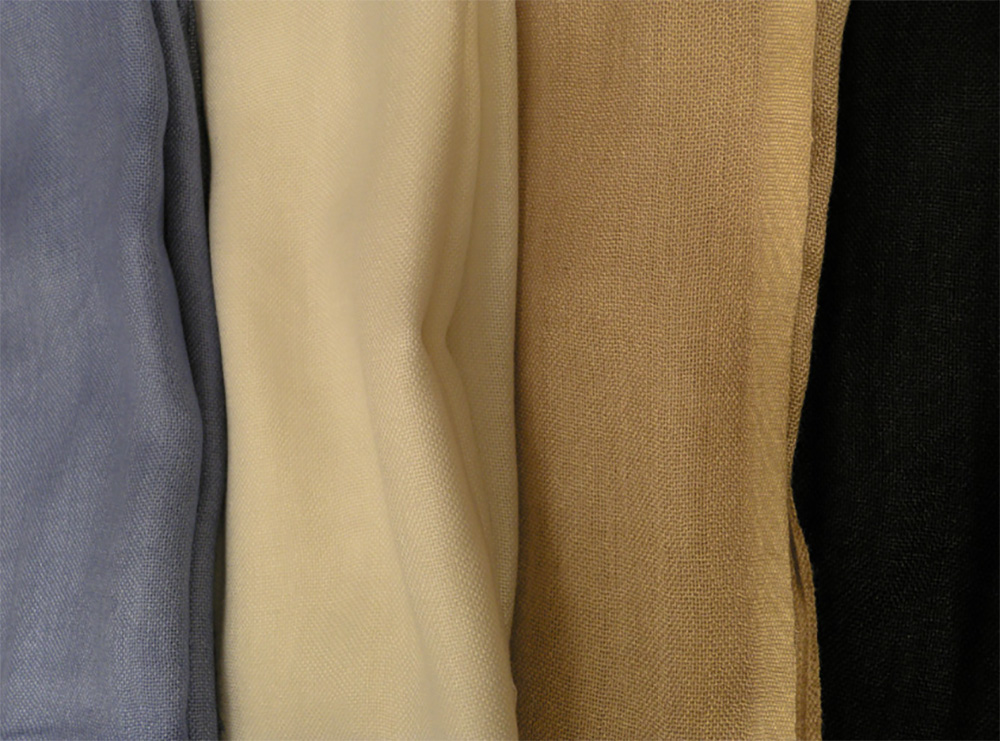
Cellulose acetate is the acetate ester of cellulose that was first manufactured at commercial scale by Celanese in 1923 starting from cellulose pulp, dissolved with acetic acid and acetic anhydride in the presence of sulfuric acid. The resulting solution is then extruded through a spinneret and the yarns are produced by solvent evaporation.
Despite the complexity of the process, cellulose acetate fibers have limited use in the textile industry because of their poor strength, poor abrasion resistance and poor thermal retention.
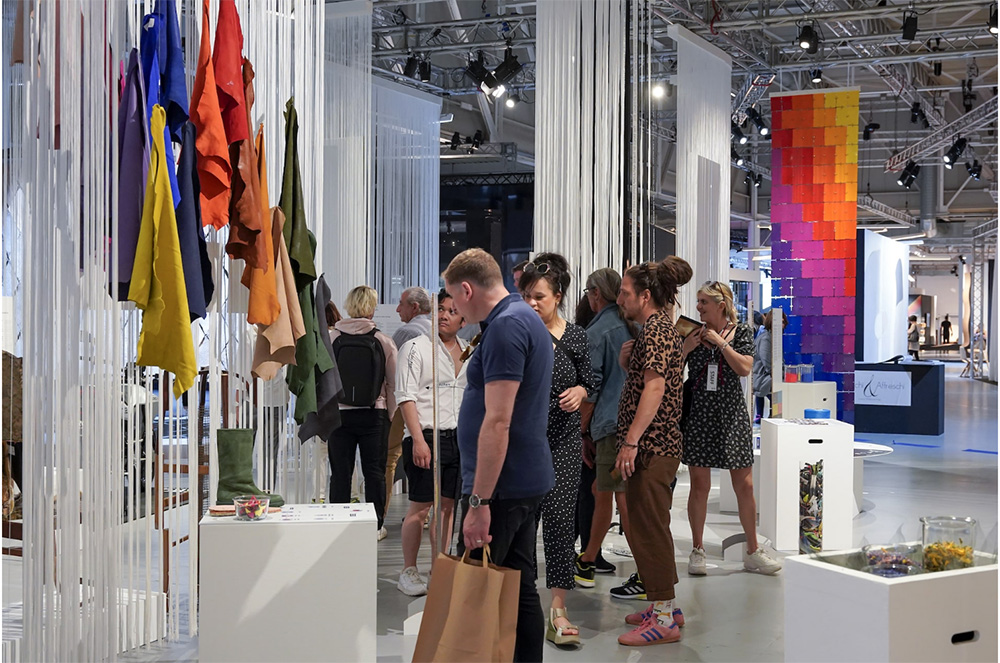
Lyocell has been until now the most successful technology of producing cellulosic fibers by direct dissolution, resulting in fibers with exceptional properties and being more environmentally friendly. Lyocell fiber has higher tenacity (especially wet tenacity), higher modulus, lower shrinkage, better thermal stability, higher crystallinity, and greater degree of orientation, than Viscose.
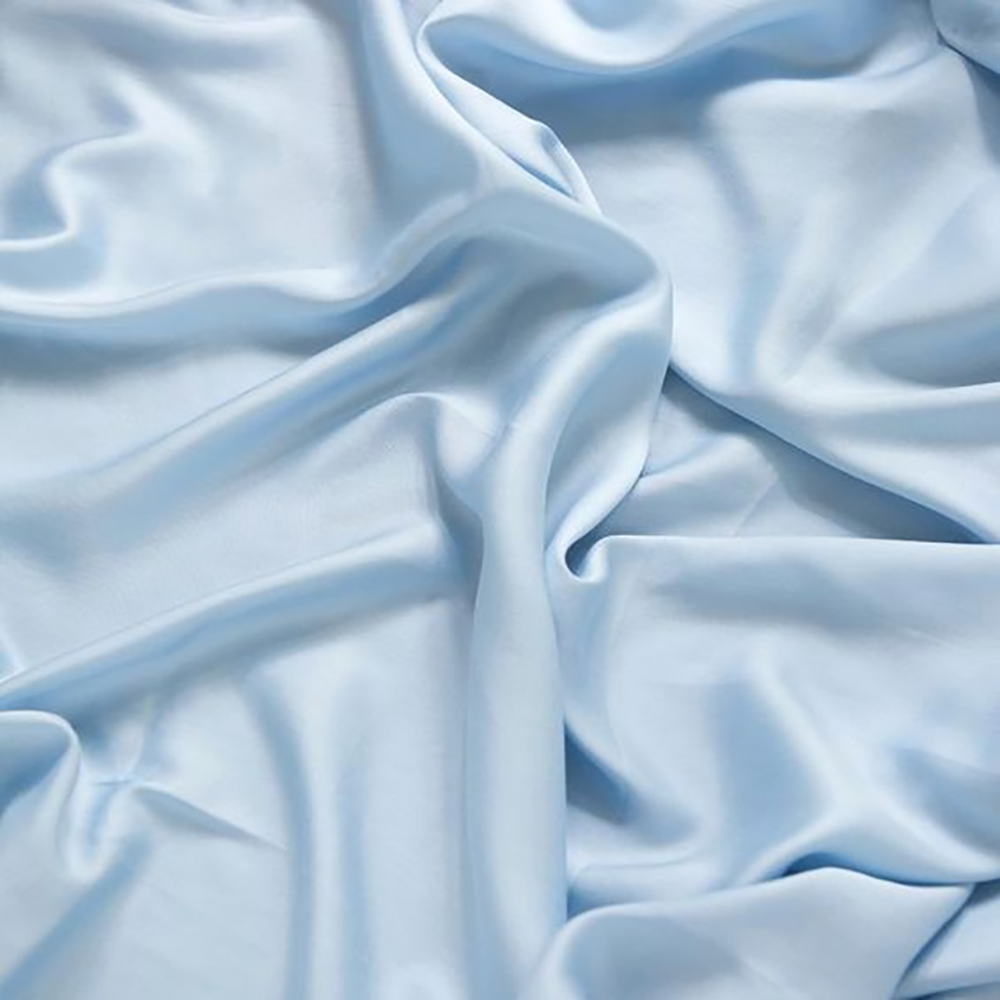
The Ioncell process is the new frontier of manufacturing cellulose-based fibers, transforming wood biomass into high-performance textile fibres. Developed by Aalto University and the University of Helsinki, the process involves the use of new, non-toxic and environmentally friendly solvents that are known as ionic liquids.
The process starts with raw recycled materials from different sources that consist in a wood-derived-biomass such cardboards, newspapers, (but also old banknotes!) and different textile waste, each containing different amounts of cellulose and lignin. Once dissolved, the cellulose is converted into strong fibers via dry-jet wet spinning method.
Being suitable to other polymers like kitosan and hemicellulose, this process opens a new world of possibilities for vegetal or biogenic derived fibers in the coming future of the textile industry.
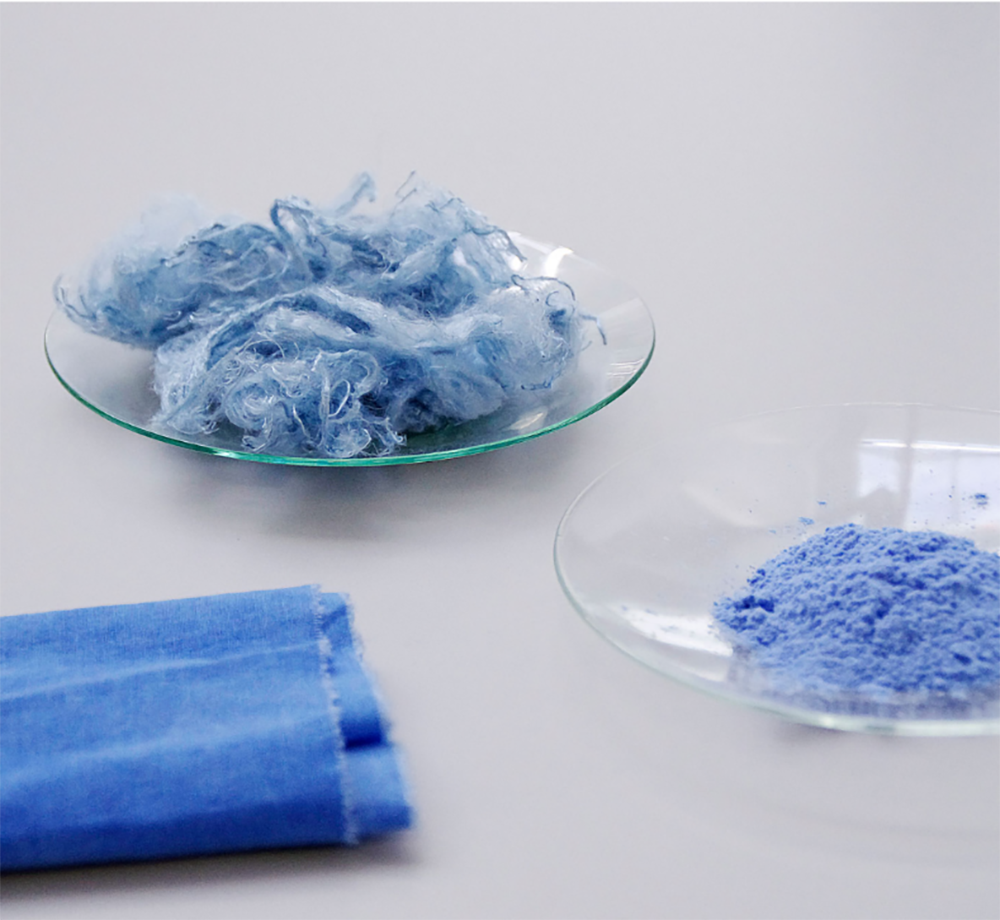
Recycled cellulose fibers and dye via the Ioncell process based on ionic liquids, www.ioncell.fi
The ionic liquids underlying the Ioncell process are further investigated and developed thanks to the European project GRETE, where Materially is also involved. The initiative, co-financed by the European Commission through the Bio-based Industries Joint Undertaking, aims to develop new technologies and processes for the production of artificial cellulosic fibers, less impacting than the solutions currently available on the market and with intrinsic properties that will allow to drastically reduce the use of water in dyeing and finishing processes.
The international collaboration that includes renowned experts among the consortium partners – as we reported in this article – will end in spring and will present the research results at the Cellulose Fibers Conference scheduled for 8 and 9 March in Cologne. Stay up to date on the developments of the GRETE project by subscribing to the newsletter